Streamline Operations
NetSuite's real-time data capabilities facilitate end-to-end visibility, ensuring operations run smoothly and efficiently by tracking every tab of data.
By leveraging ERP automation, light manufacturing companies gain powerful insights into resource allocation, production processes, and inventory management, all available at the click of a tab, crucial for maintaining competitive advantage.
The terms “real-time” and “end-to-end” are not just buzzwords but essential to your success.
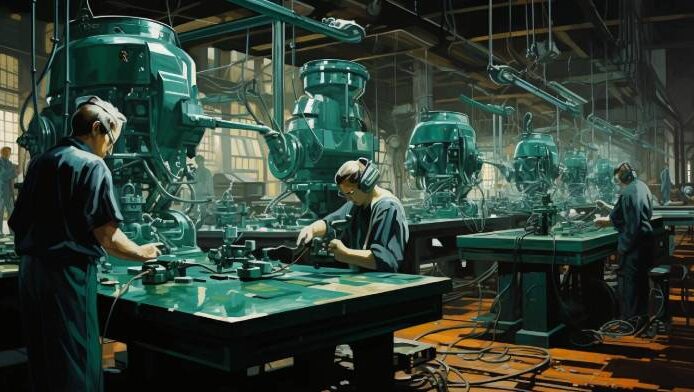
Automate Production Workflows
Enhance your light manufacturing operations with automated production workflows to ensure maximum efficiency and precision.
From raw material acquisition to final product assembly, streamlined processes allow your team to focus on innovation and quality control.
Take the next step towards operational excellence by implementing automation solutions that not only save time but also enhance overall productivity.
Real-Time Inventory Management
Accurate inventory tracking is pivotal for light manufacturing operations, minimizing stockouts, and optimizing resource use.
NetSuite eliminates guesswork by providing a unified view of inventory in real-time.
With this capability, businesses can respond quickly to changes in demand, supply chain disruptions, and production schedules.
Automated alerts help you manage reorder points and ensure optimal stock levels at all times.
Inventory discrepancies become a thing of the past, offering reliability and significant cost savings through better stock management.
Embrace real-time visibility as a strategic advantage; it's not just about efficiency, but also about driving growth.
2. Enhance Visibility
Operational transparency transforms light manufacturing, a realm of continuous improvement, where every detail matters. By leveraging NetSuite's comprehensive dashboards, businesses gain holistic insights into production cycles and resource allocation. This data-centric approach not only augments decision-making but also fortifies predictive analytics, ensuring future readiness.
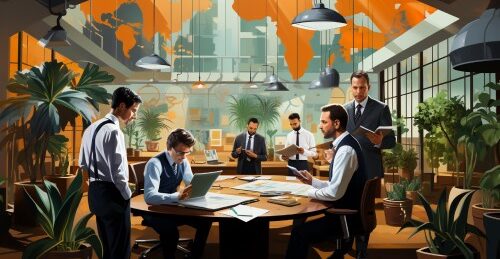
Advanced Analytics & Reporting
Transform manufacturing data into actionable insights.
Harnessing advanced analytics and reporting in NetSuite amplifies operations. The power lies in leveraging real-time data to make strategic decisions, driving operational efficiency and business growth. Consequently, businesses can identify bottlenecks, optimize resource utilization, and tailor production cycles to enhance overall performance.
Empower your team with knowledge.
Our solutions offer comprehensive dashboards and predictive analytics that convert complex data into a simplified, actionable format. These tools enable you to stay ahead of market trends and operational challenges.
In today’s competitive landscape, the importance of data-driven decisions cannot be overstated.
Centralized Data Access
Unlock streamlined processes through centralized data access.
By integrating NetSuite for light manufacturing, you ensure that all your crucial business operations are consolidated into a single, comprehensive system. This enables your teams to access real-time data across various departments, eliminating silos and fostering seamless collaboration. Consequently, your organization can respond swiftly to market demands and improve productivity.
No more fragmented systems and disjointed workflows.
With NetSuite’s centralized platform, you gain unparalleled visibility into your entire manufacturing process—from procurement to production and distribution—as it opens up comprehensive monitoring capabilities. This unified approach allows for proactive decision-making and minimizes costly disruptions.
3. Improve Compliance
Navigating the intricate landscape of regulatory requirements can be daunting for light manufacturers. NetSuite’s advanced compliance features simplify this process by providing automated updates on regulatory changes, comprehensive audit trails, and seamless reporting capabilities. Trust the SCG Team to integrate these features with precision, ensuring your manufacturing operations adhere to industry standards and statutory regulations. Contact us today to mitigate compliance risks and safeguard your business.
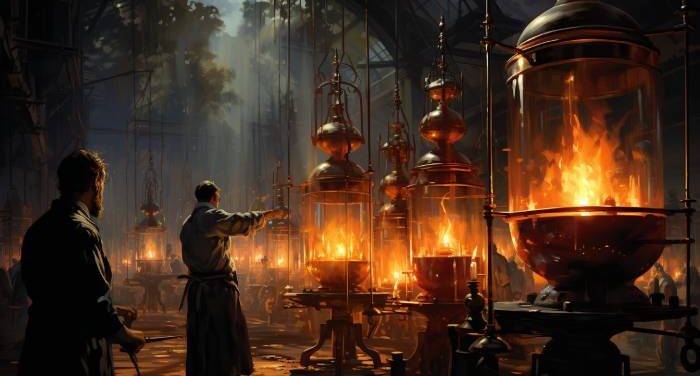
Accurate Record Keeping
Ensuring accurate record-keeping is imperative for the success of any light manufacturing business as it opens the door to streamlined audits and compliance. Precise data management allows for a seamless workflow across various functions.
NetSuite's integrated platform provides real-time visibility into all aspects of operations.
Whether it is inventory management, production scheduling, or financial reporting, NetSuite ensures precision.
Automated data entries minimize human error and maximize efficiency, ensuring your records are always up-to-date and reliable.
This meticulous approach simplifies auditing processes, compliance reporting, and strategic planning, fostering a robust operational foundation.
Ultimately, accurate records are vital for your business's growth. NetSuite's cutting-edge technology ensures that all your data remains precise and accessible.
Regulatory Standards Adherence
Navigating the complexities of regulatory standards is crucial for light manufacturing businesses to flourish.
At SCG Team, our extensive experience in tailoring NetSuite configurations to meet industry-specific standards ensures your operations adhere to the necessary regulations, significantly reducing the risk of compliance issues and penalties.
Using NetSuite, we enable seamless integration of compliance tasks directly into your daily operations. Our solutions streamline the process of maintaining regulatory standards, ensuring that your business consistently meets the required benchmarks with minimal disruption to your workflow.
4. Optimize Financials
Streamlining your financial operations is key to improving profitability, reducing costs, and enhancing overall efficiency. NetSuite's robust financial management capabilities offer real-time visibility into your financial performance, empowering you to make informed decisions and drive growth.
At SCG Team, we leverage NetSuite’s powerful tools to automate your core accounting processes, from accounts payable and receivable to tax management. By doing so, we help you achieve greater accuracy and efficiency in your financial reporting, ensuring compliance and optimizing financial performance. Contact us today to revolutionize your financial management with SCG Team's proven NetSuite strategies.
5. Cost Management Strategies
Leveraging NetSuite's capabilities, we can transform your cost management processes and drive sustainable profitability. Implementing real-time cost tracking and automated expense reporting can help you identify inefficiencies, making informed financial decisions easier.
Precise inventory management results in lower carrying costs.
Furthermore, NetSuite's customizable dashboardoffers comprehensive insights into your financial landscape, enabling a holistic view of operational expenses, budgets, and forecasts, thus allowing for prudent cost containment strategies.
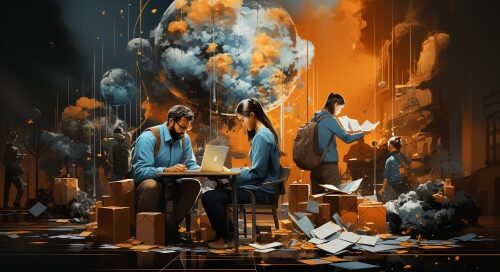
Are you ready to equip your light manufacturing enterprise for exponential growth with scalable solutions?
Since 2016, Seibert Consulting Group, a leading NetSuite consulting partner, has excelled in delivering custom solutions that drive efficiency and scalability for businesses. Our experience is rooted in hands-on implementation and real-world industry challenges.
NetSuite's inherent scalability allows your business to adapt as you grow. Whether you aim to expand your product line, enter new markets, or amplify your operational capacities, NetSuite's integrated tools support seamless growth without disruption.
Harness the power of NetSuite to streamline your operations, from inventory management to financial oversight, ensuring you maintain clarity and control at every growth stage. SCG Team's expert consultants are here to guide you through each phase of implementation and beyond.
Get a customized Demo for your business.
FAQs
How can integrated MRP software improve inventory management and purchasing processes?
Enhance Efficiency with Integrated MRP Software
In the fast-paced world of manufacturing, efficient inventory management and streamlined purchasing processes are key to maintaining competitiveness. Many companies still rely on separate systems, leading to inefficiencies such as using spreadsheets for inventory tracking or calendars for scheduling. This disjointed approach often results in disorganized procurement processes, where purchasing decisions are made based on outdated or inadequate information.
Benefits of Integrated MRP Software
- Automated Inventory Tracking – Integrated Material Requirements Planning (MRP) software automates inventory tracking, continuously updating quantities based on live data, reducing reliance on spreadsheets and manual checks.
- Streamlined Purchasing Decisions – With centralized inventory data, purchasing departments can make informed decisions. Real-time data on stock levels, pending orders, and production schedules aid in accurate forecasting and timely ordering.
- Enhanced Visibility and Coordination – MRP tools synchronize schedules and inventory levels, improving coordination across departments. This leads to better production planning and minimizes waste or shortages.
- Optimized Resource Allocation – By analyzing available materials and future production needs, MRP software helps allocate resources efficiently, reducing over-purchasing and optimizing budget management.
- Improved Vendor Management – Integrated systems track supplier performance and lead times, helping businesses build stronger relationships, negotiate better terms, and enhance procurement efficiency.
By adopting integrated MRP software, businesses can unify their manufacturing operations, significantly improving inventory management and procurement processes. This ensures materials are available when needed, optimizing production workflows and driving overall efficiency.
How does a fully integrated system benefit work order processing in manufacturing?
How Does a Fully Integrated System Benefit Work Order Processing in Manufacturing?
A fully integrated system streamlines work order processing, providing significant advantages for manufacturing operations by connecting key components like Inventory Control, Material Requirements Planning (MRP), and Bill of Materials (BOM). Here's how:
- Automated Work Order Generation – By linking sales forecasts and inventory levels, an integrated system can automatically generate work orders. This ensures that production aligns with customer demand and inventory requirements, reducing manual effort and errors.
- Real-Time Demand Awareness – Production managers gain instant insights into demand changes. When a system flags an impending "Out of Stock" scenario, managers can act swiftly to reorder materials. This real-time data helps prevent production delays, enhancing overall efficiency.
- Enhanced Workflow Management – Work orders are seamlessly connected to other modules within the software, ensuring that every department is aware of production demands. This interconnectedness promotes a cohesive workflow where bottlenecks are identified and resolved quickly.
- Improved Resource Allocation – Integrated systems provide a clear view of available supplies and production capacity. This visibility enables precise resource allocation, optimizing manufacturing for on-time and budget-friendly production.
- Facilitation of On-Time Deliveries – With synchronized work orders and effective resource management, products are manufactured and delivered on schedule. This precision in production scheduling boosts customer satisfaction and improves business outcomes.
In summary, a fully integrated system not only simplifies work order processing but also enhances the entire manufacturing workflow, making it more responsive and efficient.
What role does the Bill of Materials (BOM) play in manufacturing, and why is its integration important?
The Role of Bill of Materials (BOM) in Manufacturing
The Bill of Materials (BOM) serves as a detailed blueprint for creating a product. It lists every raw material, component, and part required to manufacture a finished item, whether it's a discrete product or a complex formulation. Each item in the BOM specifies the quantity needed, providing a clear guide for production teams to follow.
Key Roles of BOM in Manufacturing:
- Guidance for Production – The BOM provides precise instructions to ensure each product is built accurately, using the correct materials and components in the right quantities.
- Cost Estimation – By outlining every material involved, the BOM helps in calculating the total cost of production, essential for pricing strategies and profitability analysis.
- Inventory Management – A well-maintained BOM allows for efficient inventory control. By knowing exactly what's needed, manufacturers can reduce excess stock, minimize waste, and ensure that materials are on hand to meet production schedules.
- Quality Assurance – Standardizing the BOM helps maintain product consistency and quality, which is vital for customer satisfaction and meeting industry regulations.
Importance of Integrating BOM into Business Systems:
Integration of the BOM with business management solutions is crucial for seamless operations. Here's why:
- Enhanced Collaboration – Connecting the BOM with sales and purchasing systems ensures that all departments have real-time access to material requirements. This integration helps in predicting demand and streamlining procurement processes.
- Efficient Material Planning – Integrated BOM systems, together with tools like Material Requirements Planning (MRP) and Inventory Control, enable precise planning and scheduling. This synergy ensures materials are available just in time, reducing delays and keeping production lines active.
- Profitability and Efficiency – By bridging the BOM with other business functions, manufacturers can optimize resources, reduce costs, and enhance overall operational efficiency, ultimately boosting profitability.
In essence, the BOM is much more than a mere list; it's a strategic tool that, when integrated effectively, plays a pivotal role in the seamless, efficient operation of manufacturing businesses.
What are some specific industries that can benefit from light manufacturing solutions?
Industries That Benefit from Light Manufacturing Solutions
Industries across various sectors can significantly benefit from light manufacturing solutions. These industries include:
- Automotive – Companies producing automobile components, such as engine parts and interiors.
- Medical Instruments – Manufacturers of surgical equipment and health-related devices, where precision and efficiency are paramount.
- Aerospace – Firms crafting components for spacecraft and airplanes, requiring strict adherence to quality standards.
- Packaging – Businesses manufacturing everyday items like pill bottles that demand streamlined production processes.
Each of these industries relies on integrated systems to enhance efficiency and consistency in their production lines. Light manufacturing solutions optimize workflows, reduce waste, and improve product quality across the board.
What is Material Resource Planning (MRP), and why is it important for manufacturing processes?
Material Resource Planning (MRP) is a systematic approach that helps manufacturers manage and optimize inventory, production schedules, and procurement activities.
Why is MRP Important?
- Efficient Inventory Management – Ensures materials and components are available at the right time, eliminating the need for manual tracking via spreadsheets.
- Improved Production Scheduling – Integrates real-time data to create precise production schedules, preventing delays caused by outdated planning methods.
- Streamlined Procurement – Automates ordering processes based on actual demand and stock levels, reducing reliance on manual inspections and estimates.
- Enhanced Coordination and Communication – Aligns different departments, such as purchasing and production, to minimize miscommunication and improve efficiency.
Key Benefits of Implementing MRP
- Reduction in Waste – Maintains precise inventory levels to minimize excess stock and associated costs.
- Increased Efficiency – Streamlined operations reduce disruptions and accelerate production cycles.
- Cost Savings – Optimizes resources and processes to lower operational expenses.
MRP is indispensable for modern manufacturing enterprises aiming to maximize productivity while minimizing waste and inefficiencies. In an era where timely delivery and cost-effectiveness are crucial, MRP provides the tools needed to stay competitive and responsive to market demands.
What challenges does discrete manufacturing face, and how can they be managed effectively?
Challenges & Solutions in Discrete Manufacturing
Discrete manufacturing, the process of producing distinct products, comes with unique challenges that require strategic management.
Key Challenges
- Timing and Synchronization – Production schedules must align with supply chain operations to meet deadlines and customer expectations.
- Capacity Limitations – Workforce and machinery constraints can become bottlenecks, slowing production and affecting delivery schedules.
- Inventory Management – Just-In-Time (JIT) strategies require precise forecasting and coordination to minimize costs and storage needs.
- Data Accuracy – Accurate reporting is essential for monitoring production metrics and making informed decisions. Incomplete data can reduce efficiency and product quality.
Effective Management Strategies
- Optimized Scheduling – Implement advanced scheduling software to synchronize all phases of production, reducing lag times and maximizing throughput.
- Capacity Planning – Conduct regular assessments of labor and equipment capacities. Capacity planning systems can predict needs and optimize resource allocation.
- Just-In-Time Inventory – Use JIT methodologies to keep inventory levels optimized, reducing waste, lowering storage costs, and ensuring materials arrive when needed.
- Comprehensive Reporting Tools – Implement real-time reporting systems to enable quick adjustments, accurate forecasting, and improved decision-making.
By addressing these challenges with strategic planning and the right tools, discrete manufacturers can enhance productivity, reduce waste, and maintain high-quality standards.
How does process manufacturing differ from discrete manufacturing, and what complexities does it involve?
Process vs. Discrete Manufacturing: Key Differences & Challenges
Manufacturing can be broadly categorized into process manufacturing and discrete manufacturing, each with unique complexities and requirements.
Process Manufacturing: The Complexity of Consistency
Process manufacturing involves producing goods in bulk, such as food, beverages, chemicals, and pharmaceuticals. Once made, these products cannot be broken down into their original components.
Key Complexities:
- Ingredient Variability – Environmental factors impact raw material quality, requiring adjustments to maintain consistency.
- Shelf-life Management – Ingredients have limited lifespans, demanding precise scheduling to prevent spoilage.
- Environmental Factors – Temperature, humidity, and other conditions affect production, necessitating real-time adaptability.
- Regulatory Compliance – Strict industry regulations (e.g., FDA for pharmaceuticals, USDA for food) must be met.
Discrete Manufacturing: Precision and Customization
Discrete manufacturing produces distinct items like cars, furniture, and electronics, where components can be assembled and disassembled.
Key Characteristics:
- Component Assembly – Products are built from separate parts, allowing for high customization.
- Inventory Management – Tracking numerous components and parts is essential for efficiency.
- Order-based Production – Manufacturing often follows specific customer orders, requiring precise scheduling.
Why Process Manufacturing Needs Specialized Software
Due to its complexities, process manufacturing benefits from dedicated software that:
- Manages ingredient variability and adjusts formulations automatically.
- Tracks shelf-life to minimize waste.
- Ensures regulatory compliance with built-in monitoring.
- Optimizes production based on environmental conditions.
Investing in tailored software solutions helps process manufacturers streamline operations, reduce waste, and maintain high-quality standards, ensuring competitiveness in a dynamic market.
Free Consultation
Fill in the form and let us know what we can do to help on your project:
Palm Springs Headquarters
San Diego (Carlsbad) Offices